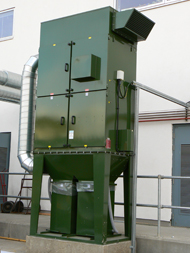
Newgate Air Systems Limited
Unit 1 Marine House
Norman Terrace
Willington Quay
Wallsend
Tyne and Wear
NE28 6SU
Malting Plant Dust Extraction & Control System
At this grain malting plant, grains of wheat and barley are processed for the distillery business. Here we were required to install a dust extraction system for the product conveyor.
The dust extraction system needs to move excess residue where the grain transfers from one conveyor to another. The plant has 5 germination units, each 28m diameter, all feeding one processing system. The conveyors have numerous extraction points to prevent dust explosion risk.
For this project we designed a dust extraction system to remove the light airborne residue from the product, which is released at each junction point on the conveyor system. There is a total of 18 extraction points for this complex system.
We designed, manufactured and installed the complete extraction system ductwork, the main dust collection unit incorporating a storage hopper, and the main extract fan assembly complete with acoustic enclosure and noise reduction silencer.
This dust extraction system installation is considered to be very successful and efficient and we are in discussions with the client regarding a further, larger dust extraction project for a larger group site.
Fume Exhaust System
One of our more challenging projects was extracting fumes from a steel profile burning process. Here we must capture fumes from a travelling fume source, the burning torch, as it moves across the whole area of the 4 x 20 metre profile burning table.
To accomplish this we developed a matrix of hoods across the width of the table. A series of dampers and limit switches direct the extraction to the immediate cutting zone. Along the length of the table we placed a lip extraction duct which is connected to a travelling burner head carriage. This permits extraction at any point along the length of the table.
![]() |
These images show the lip extraction duct and travelling burner head carriage which are described above, in a different application. Here they are being used to deal with vehicle exhaust fumes in the manufacture of heavy plant such as earthmovers and cranes. The outlet can be used at any point along the carriage, to suit the location of the parked vehicle. | ![]() |
Laboratory Fume Extraction Project
This customer had run out of lab space and so additional test rigs were located in portakabins. We designed the main exhaust systems and the internal rig cabinet extract system.
The main exhaust system will deal with 3 cabins, each has its own extraction system venting into the main one.
Electronics Clean Room Extraction
For this electronics manufacturer we designed, manufactured and installed a complete new configuration for a clean room extraction. We had to re configure the main extraction system, whilst avoiding removal of the clean air environment within the clean room facility.
We could not extract from within the room as we had to cater for ovens emitting heat. The oven exhaust flues were sealed to the oven and extended up into ceiling void, connecting to main extraction system. The system ejects into the ceiling void but has capture hoods connected so that extracted air comes out from the ceiling void.
We needed to maintain a positive pressure within the room as the air circulation system, brings in only small amount of fresh air.
Dust Explosions Risks Assessed and Safeguarded / Protected Against. Dust & Fume Extraction & Control Systems Designed, Manufactured, Installed & Maintained.
Dust & Fume Extraction Specialists – Newcastle | Sunderland | Glasgow | Aberdeen | Dundee | Edinburgh | Teesside | Middlesbrough | York | Hull | Leeds | Bradford | Huddersfield | Doncaster | Sheffield | Nottingham | Leicester | Derby | Birmingham | Manchester | Liverpool | Stoke | West Midlands | Coventry | London | Oxford | Norwich | Ipswich | Swansea | Cardiff | Yorkshire
Home | Profile | Fume Extraction | Dust Extraction | Filters | Case Studies | FAQ | Contact Us | Manufacturer Summary | Locations | Reviews | Site Map | Visit Our Blog